Pump Mechanical Seals Report Overview
The Global Pump Mechanical Seals Market was valued at USD 2,004.26 Million in 2024 and is anticipated to reach a value of USD 2,639.23 Million by 2032 expanding at a CAGR of 3.5% between 2025 and 2032.
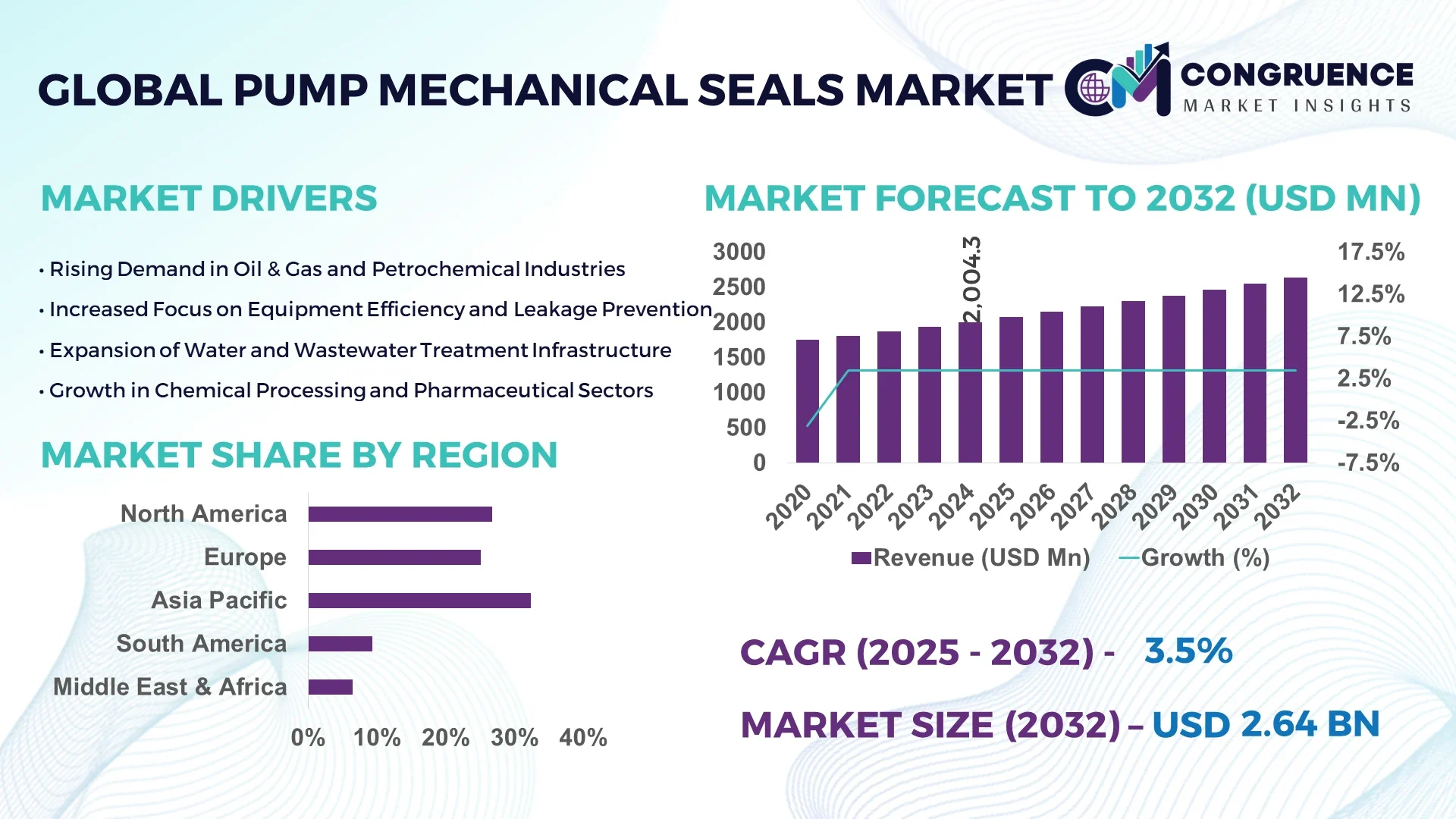
The U.S. pump mechanical seals market is showing robust growth, driven by increasing demand in industries such as oil & gas, water treatment, power generation, and chemical manufacturing. The American Petroleum Institute (API) standards are pushing companies to adopt advanced pump mechanical seals to enhance equipment life and minimize leakages. In the United States, the pump mechanical seals market benefits from high capital investments in energy infrastructure and compliance-focused upgrades in processing industries. With over 500 chemical manufacturing facilities and a resurgence in offshore oil exploration in the Gulf of Mexico, the demand for durable pump mechanical seals is rapidly increasing. Additionally, the strong emphasis on operational safety and leak prevention, aligned with federal environmental compliance, is further boosting adoption of advanced pump mechanical seals in the U.S.
How AI is Transforming Pump Mechanical Seals Market?
Artificial Intelligence (AI) is significantly transforming the pump mechanical seals market by introducing predictive maintenance, automated diagnostics, and real-time monitoring. AI-based sensors embedded in pump mechanical seals are enabling predictive analytics that detect early signs of wear, pressure loss, and seal leakage, allowing preemptive interventions before equipment failure. For instance, several industrial plants have reported a 25% reduction in unplanned shutdowns and a 30% extension in seal lifespan due to AI-enabled seal monitoring systems. Manufacturers are increasingly integrating machine learning into seal diagnostics to analyze operating conditions and optimize seal performance. In refineries and power plants, where unplanned downtime can cost millions per day, AI in pump mechanical seals ensures operational continuity and reduced maintenance overhead.
Furthermore, AI is enabling digital twin simulations for pump mechanical seals to test different stress scenarios virtually, enhancing design efficiency and custom-fit engineering. Companies in the U.S., Europe, and Asia-Pacific are rapidly shifting towards intelligent sealing systems to meet industry 4.0 requirements. AI is also enhancing energy efficiency by automating performance adjustments in mechanical seals, leading to optimized fluid handling in pumps. As AI adoption increases, the pump mechanical seals market is entering a phase of digital transformation, where smart mechanical seals become integral to predictive industrial maintenance strategies.
"In January2024, EagleBurgmann launched an AI-enabled mechanical seal monitoring platform that integrates real-time data analytics and sensor feedback to detect performance anomalies in pump seals used in refineries. This system enhances seal life by up to 30% and reduces manual inspection frequency significantly, improving overall maintenance strategies."
Pump Mechanical Seals Market Dynamics
DRIVER:
Rising demand in the pharmaceuticals and chemical industries
The increasing global production of chemicals and pharmaceuticals is driving the demand for high-performance pump mechanical seals. According to the American Chemistry Council, U.S. chemical production increased by 4.3% in 2023, directly boosting demand for industrial pumps and mechanical seals. Mechanical seals are essential in preventing hazardous chemical leaks and maintaining pressure integrity in pharmaceutical processing and chemical reactors. As regulations surrounding environmental safety and contamination control tighten, especially under FDA and EPA oversight, pharmaceutical and chemical companies are investing heavily in top-tier pump mechanical seals to ensure safe and compliant operations.
RESTRAINT:
Demand for refurbished and alternative sealing solutions
A significant challenge to the pump mechanical seals market is the growing preference for refurbished pump seals and alternative sealing technologies, especially among small and medium-sized enterprises. With rising capital expenditure concerns, many end-users are opting for used or repaired mechanical seals, which are available at nearly 40% lower cost than new ones. This cost-driven trend is particularly prevalent in developing regions of Asia, Latin America, and parts of Eastern Europe. Moreover, technologies such as magnetic drive pumps and gland packing are being re-adopted in cost-sensitive operations, restraining new pump mechanical seal installations across various industries.
OPPORTUNITY:
Expansion of wastewater treatment facilities
The global push for improved wastewater management, particularly in urban regions, is creating strong growth opportunities for the pump mechanical seals market. According to the United Nations, over 2 billion people are affected by inadequate wastewater treatment globally, and governments are investing in modernizing water infrastructure. In the U.S. alone, the EPA allocated over USD 50 billion toward water and wastewater infrastructure upgrades under the Bipartisan Infrastructure Law. These upgrades require high-reliability pump mechanical seals to prevent leakage and handle abrasive, corrosive fluids. The increased demand for clean water and sustainable treatment methods significantly opens new application areas for pump mechanical seals.
CHALLENGE:
Rising costs and operational complexity
The pump mechanical seals market faces challenges due to increasing raw material costs, particularly for carbon, ceramic, silicon carbide, and stainless steel components. Global price volatility in these materials impacts production costs and supply chain reliability. Additionally, mechanical seals require high precision and customization depending on the fluid type, pump pressure, and operational temperature, making their integration in legacy pump systems technically challenging. Complex installation, frequent alignment checks, and maintenance requirements increase downtime in facilities not equipped with trained technicians. These technical and cost-related challenges act as significant barriers for broader adoption of advanced pump mechanical seals, especially in mid-scale industrial setups.
Pump Mechanical Seals Market Trends
The pump mechanical seals market is undergoing substantial shifts, shaped by advancements in materials, regulatory pressures, and the rise of smart industrial equipment. One of the most significant trends is the adoption of non-contacting mechanical seals, which reduce wear and extend seal life by utilizing hydrodynamic or gas film technology. These seals are increasingly used in critical operations in oil & gas and chemical sectors. Another key trend is the rise of dry gas seals, particularly in compressors and rotating equipment, helping reduce fluid contamination and improve energy efficiency.
Green and energy-efficient pump mechanical seals are gaining traction as industries face environmental audits and sustainability targets. The use of low-emission and leak-proof seals is on the rise, especially in sectors like food & beverage and pharmaceuticals, where hygiene and contamination control are paramount. The increased application of modular seal designs allows faster installation and maintenance, reducing system downtimes.
Regionally, Asia-Pacific is witnessing the fastest adoption of these trends, followed by North America, driven by regulatory compliance and industrial automation. Additionally, 3D printing in mechanical seal prototyping is accelerating R&D processes, allowing custom designs for industry-specific pump applications. As these trends evolve, the pump mechanical seals market is rapidly transitioning toward high-performance, low-maintenance, and digitally integrated sealing solutions.
Segmentation Analysis
The pump mechanical seals market is segmented by type, application, and end-user industry. Each of these segments presents unique performance demands, driving specialized product innovations and adoption patterns. In terms of type, component seals, cartridge seals, split seals, gas seals, and balanced seals serve varied mechanical sealing requirements across industrial equipment. By application, centrifugal pumps, rotary pumps, reciprocating pumps, submersible pumps, and multistage pumps dominate mechanical seal usage across processing plants. End-user-wise, oil & gas, chemical processing, and water and wastewater treatment industries remain the leading consumers of pump mechanical seals. This segmentation offers a detailed understanding of how the pump mechanical seals market aligns with industry-specific demands.
By Type
-
Component Seals: Component seals are widely used in industries requiring flexible installation and easy customization of sealing elements. These seals, comprising separate rotating and stationary units, allow users to choose materials specific to application needs. In 2024, component seals accounted for over 26% of global pump mechanical seal installations, especially in the chemical and food processing industries. The flexibility to replace individual components without discarding the entire unit makes them cost-effective. The pump mechanical seals market benefits from the increasing shift toward modular equipment design, and component seals are playing a vital role in repair-friendly maintenance environments.
-
Cartridge Seals: Cartridge seals are pre-assembled units that simplify installation and alignment, reducing operational errors and enhancing sealing reliability. They dominate the pump mechanical seals market in high-pressure and high-temperature industrial applications such as oil refineries and power plants. As of 2024, cartridge seals held over 34% of the global market share. Their integrated design allows fast installation, reducing downtime by approximately 40% compared to component seals. With rising demand for plug-and-play mechanical sealing solutions in automated processing facilities, the adoption of cartridge seals is increasing significantly in both developing and developed regions.
-
Split Seals: Split seals are gaining popularity in sectors where dismantling the entire pump is not feasible for maintenance. These seals are ideal for large pumps used in wastewater treatment and pulp & paper industries. In 2024, split seals contributed to about 11% of the global pump mechanical seals market. Their ability to be installed without removing the motor or coupling significantly lowers maintenance time and costs. These advantages are driving their uptake, particularly in North America and Europe, where aging infrastructure and large pump systems dominate water treatment applications.
-
Gas Seals: Gas seals use a gas barrier instead of liquid and are mainly employed in clean, dry, and high-speed processes, especially in compressor applications. These seals offer lower friction and heat generation, leading to extended equipment life. In 2024, gas seals represented around 8% of the total pump mechanical seals market. Their popularity is increasing in sectors like pharmaceuticals, where contamination-free operations are essential. The trend toward emission control and leak prevention in hazardous chemical handling further drives the adoption of gas seals in both developing and industrialized economies.
-
Balanced Seals: Balanced seals are designed to handle high-pressure and high-temperature media, offering reduced face loading and extended seal life. These seals are commonly used in oil refineries, petrochemical, and thermal power plants. In 2024, balanced seals held approximately 21% of the pump mechanical seals market. Their ability to manage high-pressure differentials without excessive heat generation makes them ideal for heavy-duty applications. With rising energy demand and refinery throughput, the adoption of balanced seals is expected to remain strong, especially in Asia-Pacific and the Middle East.
By Application
-
Centrifugal Pumps: Centrifugal pumps represent the largest application segment in the pump mechanical seals market, owing to their extensive use in industrial, commercial, and municipal settings. In 2024, centrifugal pumps accounted for over 45% of all mechanical seal applications. These pumps rely heavily on high-integrity sealing systems to prevent leakage and maintain process safety. Industries such as oil & gas, water treatment, and HVAC systems are leading adopters of centrifugal pumps, driving high-volume mechanical seal demand. Continuous innovations in seal design to support variable speed centrifugal pumps are further propelling the segment’s dominance.
-
Rotary Pumps: Rotary pumps utilize positive displacement to handle viscous fluids, making mechanical seals essential for containing high-pressure differentials. In 2024, rotary pump applications comprised about 19% of the total pump mechanical seals market. These pumps are widely used in petrochemical, lubrication, and food-grade applications. Mechanical seals in rotary pumps must ensure leak-proof operation while handling sticky and corrosive fluids. The rising adoption of rotary lobe and gear pumps in chemical and biofuel processing has increased demand for specially coated mechanical seals that resist wear and chemical attack.
-
Reciprocating Pumps: Reciprocating pumps use a piston mechanism and are typically used in high-pressure environments such as chemical dosing and oil extraction. These applications require mechanical seals capable of withstanding pressure surges. In 2024, about 12% of mechanical seal installations were in reciprocating pump systems. Seals in this category need to maintain tight tolerances under severe duty cycles. As reciprocating pump usage rises in shale gas exploration and offshore operations, demand for durable mechanical seals that reduce vibration-induced wear is increasing rapidly.
-
Submersible Pumps: Submersible pumps are deployed in underwater conditions, requiring mechanical seals that provide complete fluid isolation and corrosion resistance. These are widely used in water treatment, mining, and agricultural irrigation. In 2024, submersible pumps accounted for 14% of the mechanical seal application segment. Seals in these systems often use elastomers and ceramics to resist sand, debris, and chemical corrosion. Rising groundwater extraction and infrastructure investments in emerging markets are fueling the expansion of mechanical seals specifically engineered for submersible pumps.
-
Multistage Pumps: Multistage pumps generate high head pressure, requiring robust mechanical seals to manage high differential pressures and thermal expansion. These pumps are common in boiler feedwater systems, desalination plants, and high-pressure chemical transfers. As of 2024, they contributed to about 10% of mechanical seal applications globally. Mechanical seals for multistage pumps often feature dual sealing systems and advanced pressure-balancing features. Increasing deployment in thermal power generation and industrial desalination is expanding the demand for reliable mechanical sealing in multistage pump configurations.
By End-User Insights
-
Oil & Gas Industry: The oil & gas industry remains the largest end-user of pump mechanical seals, with sealing systems essential for pipelines, refineries, and offshore rigs. In 2024, this sector represented approximately 39% of the total market. The need for zero-emission systems in volatile fluid processing and the expansion of LNG infrastructure continue to drive mechanical seal innovation. Increasing upstream and downstream activities in the Middle East and North America are further strengthening the segment. Mechanical seals in this sector must endure high pressures, corrosive media, and extreme temperatures, requiring superior-grade materials and performance-enhancing coatings.
-
Chemical Processing Industry: In the chemical processing industry, pump mechanical seals are critical for handling aggressive, corrosive, and hazardous chemicals. In 2024, this sector held about 28% of the global market share. The growing demand for specialty chemicals, fertilizers, and industrial solvents has led to higher demand for seals that offer chemical resistance, longevity, and operational safety. The shift toward closed-loop, emission-controlled chemical processing facilities in Europe and Asia is also fueling adoption. Mechanical seals in this segment are increasingly being integrated with monitoring technologies to detect micro-leakages and improve safety compliance.
-
Water and Wastewater Treatment: Water and wastewater treatment facilities rely heavily on pump mechanical seals to prevent fluid leakage and maintain hygienic operations. In 2024, this sector contributed to over 19% of the pump mechanical seals market. The rising implementation of desalination and wastewater recycling plants across the Asia-Pacific and Middle East regions is driving demand for corrosion-resistant and long-lasting mechanical seals. Seals used in this segment must endure high levels of abrasion and continuous exposure to sludge, chemicals, and contaminants. Increasing global focus on sustainable water infrastructure is expected to further bolster seal deployments in this end-user industry.
Region-Wise Market Insights
The Asia-Pacific region accounted for the largest market share at 32.4% in 2024; however, Middle East & Africa is expected to register the fastest growth, expanding at a CAGR of 4.1% between 2025 and 2032.
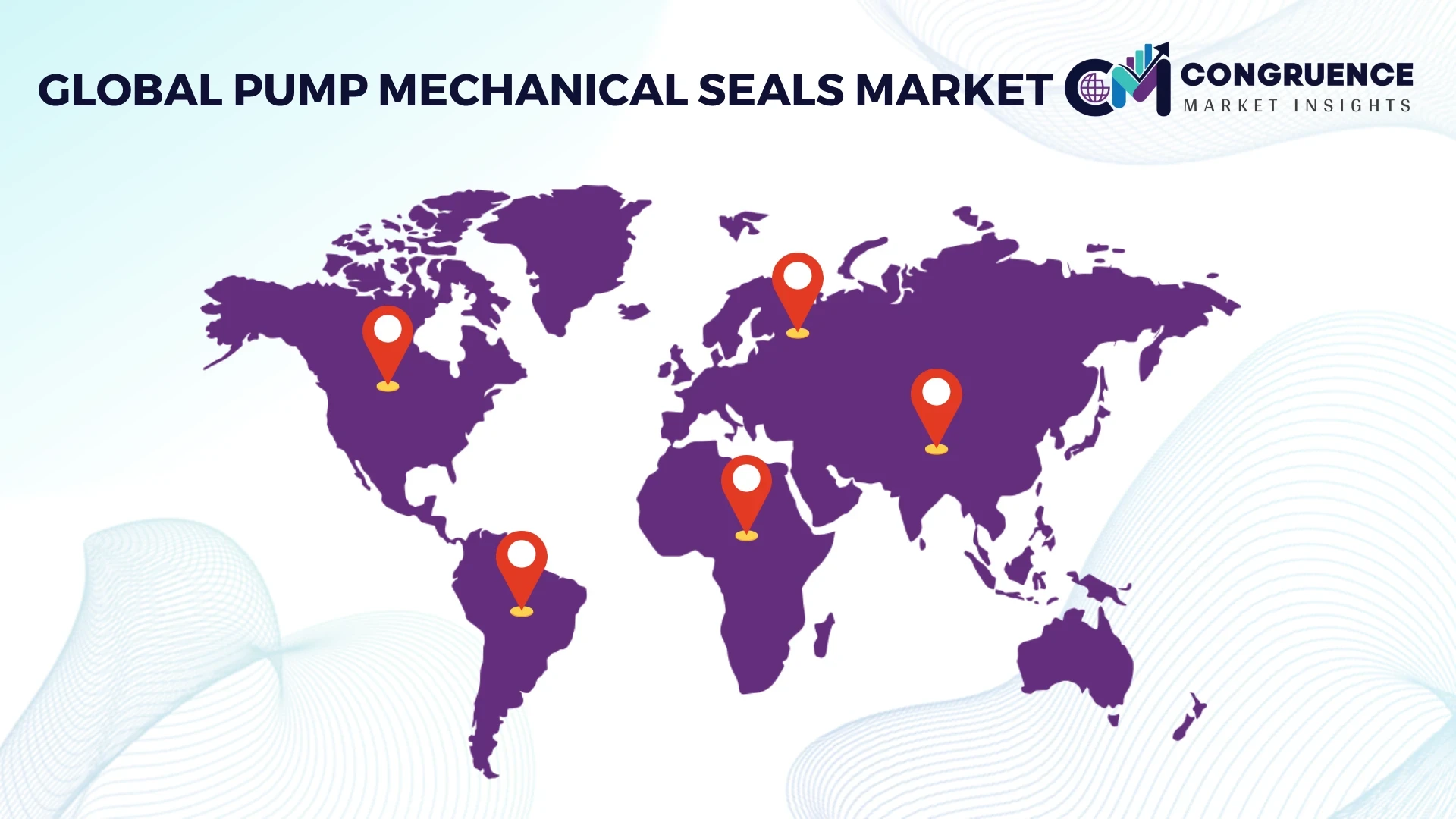
The pump mechanical seals market in Asia-Pacific is primarily driven by increasing demand for water and wastewater treatment infrastructure, rapid industrialization, and growing investments in the chemical and oil refining sectors across China, India, and Southeast Asia. In North America, the presence of key manufacturing hubs and high adoption of rotary and centrifugal pumps are contributing to a steady demand for pump mechanical seals. Europe is focusing on sustainability and renewable energy applications, which has supported the uptake of balanced and cartridge seals in water-intensive industries. The Middle East & Africa region is witnessing significant spending on desalination and oil & gas projects, which is directly contributing to the increased installation of mechanical seals in submersible and multistage pump systems.
North America Pump Mechanical Seals Market Trends
Advanced Oilfield Services and Retrofit Solutions Boost Market Penetration
The North America pump mechanical seals market is being bolstered by growth in the shale gas and oil sectors, particularly in the United States and Canada. There are over 9000 operational oil and gas extraction facilities in the region, many of which are upgrading their systems with modern mechanical seals to reduce emissions and improve operational efficiency. Moreover, retrofit solutions for aging centrifugal and reciprocating pumps have become a major revenue stream, especially for OEMs offering component and cartridge seal systems. The water and wastewater sector is also witnessing modernization efforts, boosting demand for split and balanced seals in government-led treatment projects. Strong regulatory compliance and emphasis on energy-efficient sealing solutions are further accelerating growth in the North America pump mechanical seals market.
Europe Pump Mechanical Seals Market Trends
Emission Control Standards Propel Demand for High-Efficiency Seals
In Europe, the pump mechanical seals market is driven by stringent environmental regulations focused on reducing equipment leakage and improving safety. The European Commission’s industrial emission standards mandate the use of high-integrity mechanical seals in sectors like food processing, chemical manufacturing, and wastewater treatment. Germany, the UK, and France are leading the charge with strong adoption of cartridge and split seals in automation-intensive industries. Additionally, the presence of key manufacturers and seal technology centers across Scandinavia and Western Europe ensures a steady supply of customized sealing solutions. Retrofits in legacy plants, particularly in the chemicals and pharmaceuticals industries, are pushing demand for balanced seals designed for volatile fluid handling. Europe remains a mature but evolving market for pump mechanical seals, with sustainability acting as a critical market driver.
Asia-Pacific Pump Mechanical Seals Market Trends
Industrial Infrastructure and Population Growth Stimulate Demand
The Asia-Pacific pump mechanical seals market is rapidly growing due to surging industrial development, infrastructure expansion, and the increasing demand for safe water systems. China, India, Indonesia, and Vietnam are leading in industrial expansion, particularly in textiles, chemicals, and paper industries, which use centrifugal and multistage pumps with advanced sealing systems. In 2024, Asia-Pacific contributed over 32.4% of the global pump mechanical seals market volume. Government-led initiatives in wastewater management and desalination across urban centers have further increased adoption of component seals and gas seals in large-scale pump installations. With urban population growth and rising per capita water demand, utility providers in the region are investing in high-performance mechanical seals that reduce maintenance and improve energy efficiency.
Middle East & Africa Pump Mechanical Seals Market Trends
Mega Projects in Oil, Gas, and Water Fuel Expansion in MEA Region
The Middle East & Africa pump mechanical seals market is expanding due to major investments in energy and water infrastructure. In 2024, the region contributed around 8.9% of the global market and is set to grow at the fastest pace through 2032. Countries such as Saudi Arabia, UAE, and Egypt are deploying pump mechanical seals in large-scale desalination, petrochemical, and refinery projects. The ongoing Neom city project and Vision 2030 in Saudi Arabia have created unprecedented demand for multistage and submersible pump seals. Balanced and gas seals are in high demand for oilfield applications where fluid integrity and operational safety are paramount. The mining and metals sectors in South Africa are also driving demand for rotary pump seals in slurry and fluid transfer applications.
Market Competition Landscape
The pump mechanical seals market is highly competitive, with global and regional manufacturers focusing on innovation, customization, and lifecycle solutions to maintain a competitive edge. Players are investing in R&D to develop high-performance cartridge seals, dry gas seals, and split seals for harsh industrial applications such as oil refineries, chemical reactors, and submersible wastewater pumps. Mergers and acquisitions have increased, with several companies expanding their service offerings through digital monitoring systems and seal reliability programs. For instance, firms now provide predictive maintenance analytics integrated with seal monitoring, which reduces downtime in large-scale pump installations. The emergence of AI-based diagnostic tools is further intensifying competition among suppliers offering smart sealing systems. Market leaders also differentiate through extensive aftermarket support, seal refurbishment centers, and rapid deployment capabilities. The competitive environment is marked by the presence of both multinational engineering companies and specialized sealing technology providers that compete on pricing, quality, and service responsiveness.
Companies Profiled in the Pump Mechanical Seals Market Report
-
Flowserve Corporation
-
John Crane (a division of Smiths Group)
-
EagleBurgmann
-
AESSEAL
-
Sulzer Ltd
-
Ekato Group
-
Trelleborg Sealing Solutions
-
Parker Hannifin Corporation
-
James Walker Group
-
Garlock Sealing Technologies
-
Roplan
-
Flex-A-Seal, Inc.
-
Meccanotecnica Umbra
Technology Insights for the Pump Mechanical Seals Market
The pump mechanical seals market is undergoing significant technological advancements, focusing on enhancing performance, sustainability, and operational efficiency. One notable development is the integration of smart mechanical seals equipped with IoT capabilities. These seals can monitor parameters such as temperature, pressure, and vibration in real-time, facilitating predictive maintenance and reducing unplanned downtime. This technology is particularly beneficial in industries like oil and gas, where equipment reliability is paramount.
Another innovation is the adoption of advanced coatings, such as diamond-like carbon (DLC) and ceramic coatings, which enhance the durability and wear resistance of mechanical seals. These coatings are especially useful in harsh operating environments, extending the service life of seals and reducing maintenance costs.
The use of high-performance elastomers like Viton and EPDM is also on the rise. These materials offer excellent resistance to heat and chemicals, making them suitable for demanding applications in chemical processing and water treatment.
Furthermore, the industry is witnessing a shift towards eco-friendly and sustainable seal materials. Manufacturers are focusing on recyclable and non-toxic materials that meet environmental standards without compromising performance.
Additive manufacturing (AM) or 3D printing is emerging as a transformative technology in the production of mechanical seals. This approach allows for rapid prototyping and customization, reducing production time and costs. For instance, some manufacturers have achieved up to 75% reduction in turnaround time by adopting 3D-printed mechanical seal components.
Lastly, the development of sealless pumps, which eliminate the need for mechanical seals by using magnetic drive systems, is gaining traction. These pumps offer a hermetic seal, making them ideal for handling hazardous or toxic fluids, and are increasingly adopted in the chemical and pharmaceutical industries.
Recent Developments in the Global Pump Mechanical Seals Market
-
In June 2024, a company introduced the ETHERLINE® FD bioP Cat.5e, its first bio-based Ethernet cable produced in series. This sustainable variant features a bio-based outer sheath composed of 43% renewable raw materials, reducing the carbon footprint by 24% compared to traditional fossil-based TPU sheaths.
-
In April 2024, a leading manufacturer launched Diamond® Seal Face Technology, featuring a specialized low-friction, high-durability face coating. This innovation enhances seal longevity and supports reliable equipment operation even in harsh conditions.
-
In March 2024, a global seal producer collaborated with a metal processing firm to manufacture 3D-printed mechanical seals, achieving a reduction in turnaround time by up to 75%. This partnership leverages additive manufacturing to enhance production efficiency.
-
In January 2024, a sealing technology company introduced advanced mechanical seals with improved designs and materials, including advanced ceramics and high-performance polymers. These enhancements offer better resistance to wear and corrosion, addressing the evolving needs of various industries.
-
In December 2023, an industrial solutions provider introduced the Sense Turbo, an innovative digital diagnostics solution for dry gas seals in compressors. This technology monitors and assesses operational conditions within the core of the compressor system, enhancing reliability and efficiency.
Scope of Pump Mechanical Seals Market Report
The Pump Mechanical Seals Market Report provides a comprehensive analysis of the global market, focusing on various types of seals, applications, end-user industries, and regional trends. It examines the market dynamics, including drivers, restraints, opportunities, and challenges that influence market growth. The report delves into technological advancements, such as the integration of IoT in mechanical seals, the use of advanced coatings, and the adoption of high-performance elastomers. It also highlights the shift towards eco-friendly materials and the emergence of additive manufacturing in seal production. The report covers key applications across industries like oil and gas, chemical processing, water and wastewater treatment, and power generation. Regional analysis includes insights into market trends in North America, Europe, Asia-Pacific, and the Middle East & Africa. The competitive landscape section profiles major players, detailing their product offerings, strategic initiatives, and market positioning. Overall, the report serves as a valuable resource for stakeholders seeking to understand the current state and future prospects of the pump mechanical seals market.
Pump Mechanical Seals Market Report Summary